Shaw 35 MC Urethane Wood Adhesive
Description
Shaw 35 MC is Shaw’s premium, 100%-solids, one-component, moisture-curing urethane adhesive for all types of wood flooring. Shaw 35 MC can be used in a single-coat application that provides superior bond and moisture vapor emission control on concrete slabs. No moisture testing required when installed according to the following instructions. Shaw 35 MC also provides sound reduction properties.
Features and Benefits
- Moisture barrier, sound reduction and bonding system in a single product.
- 100%-solids; no solvent added.
- Utilizes rapidly renewable raw materials.
- Low-odor formula with negligible VOC content.
- May be used below grade with engineered wood.
Environmental
-
California South Coast Air Quality Management District Rule 1168
-
California Department of Public Health Section 01350
-
CRI Green Label Plus Certified 100128
LEED IEQ Credit Information (2009 and V4)
Credit Requirement
|
Status
|
Comment
|
Meets General Emissions Evaluation Criteria
|
Complies
|
CRI Green Label Plus (GLP) #100128
|
VOC’s (Rule #1168 of California SCAQMD amended October 6, 2017)
|
Complies
|
VOC Content < 20 g/L
|
Limitations
- Do not install over any substrates containing asbestos.
- For interior installations only.
- Do not apply over any adhesive residues including cutback adhesive.
- Not recommended for flooring designed for nail-down installations only
- Not recommended for prefinished cork flooring.
- Install flooring only in areas recommended by the wood-flooring manufacturer.
- Shaw 35 MC is effective at protecting the flooring from moisture through the concrete, however it will not protect from environmental moisture such as flooding, leaks, wet mopping or spills.
- Do not install if standing water is observed on the surface of any substrate.
- Do not install in areas with known hydrostatic moisture problems.
- Do not install if the substrate has a glass-like surface.
- Patch and level with exterior-rated, cement-based products only.
Use
- Approved for use with solid and engineered exotic and domestic wood flooring of any width and length; finger block parquet; acrylic impregnated wood and laminated plank; bamboo; and reground rubber or cork underlayments.
- For all Interior use.
Suitable Substrates
- Porous concrete that has been installed at least 14 days.
- Properly prepared cement terrazzo.
- Exterior-grade plywood and other approved wood substrates (per wood-flooring manufacturer recommendations). Note: Moisture-barrier properties do not apply to installations over wood underlayments.
- Existing, properly prepared ceramic tile as long as glazed surfaces are abraded.
- Exterior-rated, cement-based self-leveling underlayments and patching compounds.
- Properly prepared, primed gypsum underlayments that meet the requirements for compressive strength according to ASTM F2419. Note: Moisture-barrier properties do not apply to installations over gypsum underlayments.
- Radiant-heat systems that have been properly installed.
Note: Moisture-barrier properties do not apply to installations over radiant-heat systems.
Subfloor Preparation
- All substrates must be structurally sound, dry, solid and stable, dry to the touch with no visible standing water.
- The substrate should be clean and free of dust, dirt, oil, grease, paint, curing agents, concrete sealers, loosely bonded toppings, loose particles, and any other substance or condition that may prevent or reduce adhesion.
- Substrates must be flat to 3/16” in a 10-ft. span (4,5 mm in a 3,05-m span).
- Concrete surfaces must be porous. Do not install over extremely smooth, non-porous or glass-like concrete surfaces. If the substrate is glass-like or non-porous, it must be mechanically profiled and prepared by shotblasting, sandblasting, water jetting, scarifying or other engineer-approved methods to an International Concrete Repair Institute (ICRI) concrete surface profile (CSP) #2 to #3 standard. Note: Diamond grinding is an approved method for subfloor preparation in small areas that are not accessible by the methods mentioned above.
- Concrete and exterior-rated, cement-based underlayments/patches must be cured and free of any hydrostatic and/ or moisture problems.
For questions, please contact Shaw technical service at 1.800.257.7429.
Conditions Of Use
Substrate temperature should be between 65° F (18°C) and 90°F (32°C).
Mixing
- Ready to use; no mixing required
- Note: Choose all appropriate safety equipment before use. Refer to Material Safety Data Sheet (MSDS) for more information.
Product Application
- Read all installation instructions thoroughly before installation.
- Refer to the wood-flooring manufacturer’s guidelines for acclimation requirements and complete installation instructions.
- Remove the clip-on trowel attachments found inside the pail. See chart below to select proper trowel.
- Using a generous amount of adhesive, key the adhesive into the subfloor using the flat side of the trowel forming a continuous film of adhesive.
- Once the adhesive has been keyed in, immediately spread the adhesive using the provided clip-on trowel. Trowel ridge lines should be perpendicular to the wood-flooring installation direction. Hold the trowel at a 60° to 90° angle to the subfloor, making sure that the subfloor is covered 100% with adhesive and no void spots appear other than the “valley bottoms” created by the trowel. These areas will fill in as the wood is installed.
- Only apply as much adhesive as can be installed in 45 minutes.
- Install flooring in strict accordance with the flooring manufacturer’s written instructions.
- Install the wood flooring immediately, pressing firmly into the adhesive to ensure 100% coverage of the subfloor and transfer to the wood flooring backing.
- Roll with 100 pound roller to insure wood is totally seated into the adhesive.
- Use a new clip-on trowel blade with each pail of adhesive. A new blade is provided with each pail.
- Protect from light traffic for at least 12 hours. Protect from heavy traffic for at least 24 hours.
Cleanup
Clean any adhesive smudges immediately using a solvent-based urethane cleaner. Clean while adhesive is still fresh or wet.
NOTE: Shaw 35 MC is extremely difficult to remove when cured.
Do not use water to remove adhesive or adhesive residue.
Protect From Freezing
Freeze/thaw-stable up to 5 cycles at 0°F (18°C). Store at room temperature in a dry area.
Product Properties
Polymer type |
Moisture-cured Polyurethane |
Percent solids |
100% |
Odor |
Light and sweet |
Density |
14 lbs. per U.S. gal. (1,69 g per mL) |
Color |
Off-white |
Flash point (Tag) |
> 200ºF (93ºC) |
Shelf life |
1 year when stored in original, unopened package at 73°F (23°C) |
Perm rate (ASTM E96) |
>0.15 perm |
ASTM Standards for Sound Reduction: The following sound tests (for tile and wood flooring) were conducted and results supplied by NGC Testing Services, Buffalo, NY
Sound-Reduction Ratings – Engineered Wood 3/8” (10 mm) Thick Over 6” (15 cm) Concrete Slab
ASTM Test Method |
No Suspended Ceiling |
Suspended Gypsum Ceiling |
ASTM E90-09/E413-04 (STC)
Airborne sound |
50 (NGC Test No: 5010020) |
67 (NGC Test No: 5010019) |
ASTM E492-09/E989-09 (IIC)
Impact Sound |
50 (NGC Test No: 7010034) |
68 (NGC Test No: 7010037) |
ASTM E2179-03 (Delta IIC)
Impact Sound |
21 (NGC Test No: 7010035) |
NA |
APPROXIMATE PRODUCT COVERAGE* |
Trowel |
Coverage |
For engineered wood flooring more than 3/8” (10 mm) in thickness and 3/4” (19 mm) or less in thickness: V-notch with lift spacers – 3/8”x 3/16”x 3/8”x 1/16” (10 x 4,5 x 10 x 1,5 mm)
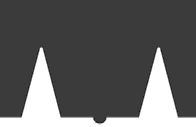 |
Up to 30 sq. ft. per U.S. gal (0,73 m2 per L) |
For engineered wood flooring of 3/8” (10 mm) or less in thickness: V-notch with lift spacers – 1/8” x 1/8” x 1/8” x 1/16” (3 x 3 x 3 x 1,5 mm)
Use a new clip-on trowel blade with each pail of adhesive. A new blade is provided with each pail.
|
Up to 36 sq. ft. per U.S. gal. (0,88 m2 per L) |
* Trowel dimensions are depth/width/space/lift. Coverage shown is for estimating purposes only. Actual jobsite coverage may vary according to substrate conditions, type of trowel used and setting practices.